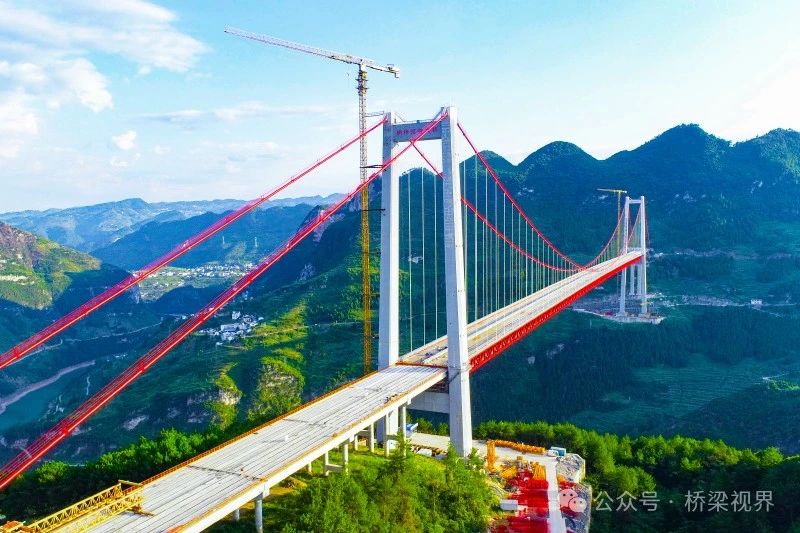
Project Profile
Name: Tongzhe River Grand Bridge
Status:Under construction
Location: Guizhou
Length: Total bridge length 1422m, main span 965m
Type: Suspension bridge
Feature: Tongzhe River Grand Bridge is a large-span suspension bridge designed with high and low towers and without pile foundations
Project Stakeholders: Developer: Guizhou Expressway Group Co., Ltd., China Railway Development & Investment Group Co., Ltd.
Designer: China Railway Major Bridge Reconnaissance & Design Institute Co., Ltd.
Contractor: China Railway Guangzhou Engineering Group Co., Ltd.
Supervisor: Guizhou Lutong Engineering Management Consulting Co., Ltd.
The Tongzhe River Grand Bridge is located at the border of Renhuai City and Tongzi County, spanning the Tongzhe River. It has a total length of 1422 meters, with a main span of 965 meters and a main tower height of 208 meters. The main bridge is a double-tower single-span steel truss suspension bridge, making it the largest span and most challenging construction project on the Jin-Ren-Tong Expressway in Guizhou.
Unique Features:
- Rare structural combination form in China
The bridge’s anchorage system simultaneously adopts tunnel anchors and gravity rock-socketed anchors. The high and low towers on both banks respectively use pile group foundations and expanded foundations. The main cables use 1960MPa high-strength galvanized aluminum parallel steel wires, optimizing the number of cable strands from 114 in the preliminary design to 91. The steel truss is designed with corbels to suspend the permanent hanging points outside the main truss (steel beam deck width 29m, hanging point spacing 26m, main truss spacing 23.5m). This structural combination is rare in China.
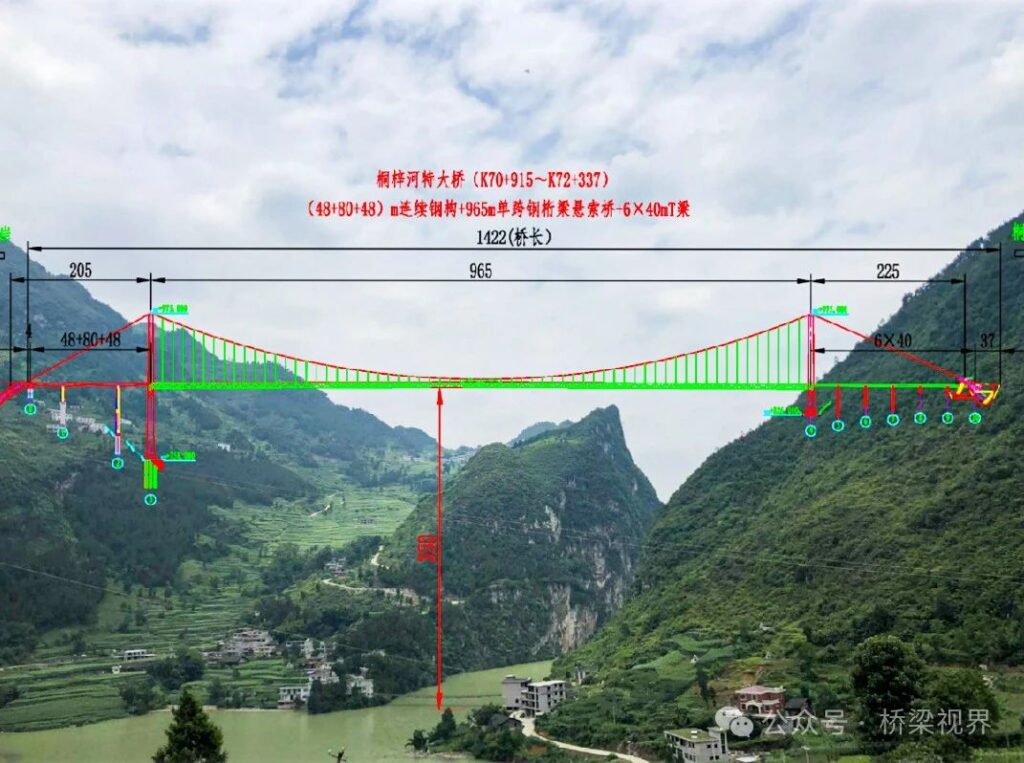
- Key line points are significantly constrained by external environment
The 208-meter high tower and tunnel anchor on the Renhuai side are the schedule-controlling parts of the entire bridge, but the Renhuai side simultaneously faces four major challenges: (1) Demolition of 12 houses on the main pier slope (2) Local road crossing the construction area (3) Excavation work in geological disaster areas (4) Extremely poor 12-kilometer access road conditions affecting over 500 village households.
- Complex and winding temporary roads, difficulty in transporting large materials
(1) The bridge site is surrounded by villages, with existing narrow roads passing through settlements, steep slopes, and small turning radii, making it difficult for construction vehicles to pass and transport materials. The two sides of the bridge are separated by the Tongzi River, requiring a 160-kilometer detour using existing roads, severely affecting construction management and communication between the two sides. Thus, two independent work areas are set up.
(2) High local population density, difficult group work
(3) The bridge sites on both banks are located within local villages, with dense housing, population, and farmland nearby. The local people are relatively bold, resulting in much greater safety protection, coordination, guidance, and compensation during construction compared to other similar projects, increasing construction difficulty.
Innovations
- Raising the cap elevation on the Renhuai side to reduce slope excavation
The bridge site area of this project is a typical deep-cut “V”-shaped valley of the Tongzi River, with intense river valley cutting and steep terrain on both sides, often forming steep cliffs. The vegetation on both banks is well-developed. The Renhuai side mountain slope is steep, with natural slope angles of 30° to 50°, exposed bedrock, visible steep limestone at the upper part of the mountain, and mudstone interbedded with shale at the lower part. Through design optimization work during the project preparation period, fully considering the impact of main structure construction on the environment, the elevation of the cap platform on the Renhuai side was raised, significantly reducing the excavation range and volume, saving costs while reducing damage to the natural topography and geomorphology of the mountain.
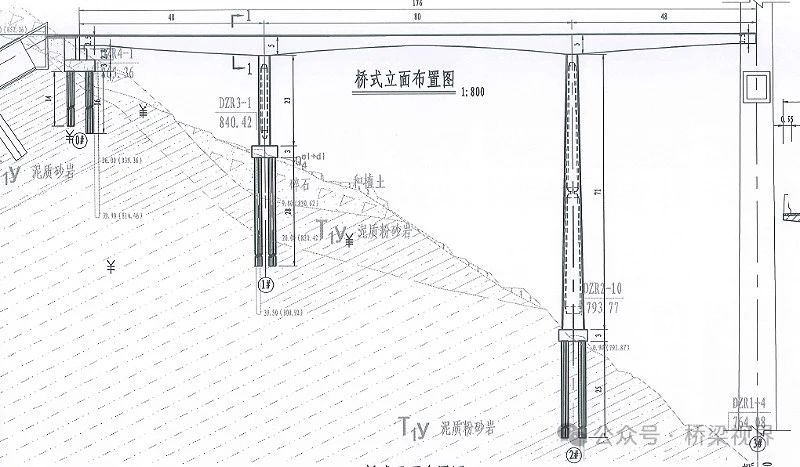
- Anchor bolt anchorage frame beam + vegetation bags for high slopes on the Renhuai side
The main pier on the Renhuai side is located in a fractured landslide area of the mountain, which has been assessed as a geological disaster area by the local government. For this geological disaster area on the Renhuai side, 7 anti-slide piles were set up at the tunnel anchor entrance from top to bottom, and the lower slope adopted anchor bolt anchorage frame beam protection. A 15m high lightweight mixed bubble soil retaining wall was set up at the bottom of the main tower for slope protection, ensuring the main structure construction under complex geological conditions on the Renhuai side. The entire construction process had a very small impact range on the mountain, and the project won the Guizhou Province and China Railway Green Demonstration Project awards.
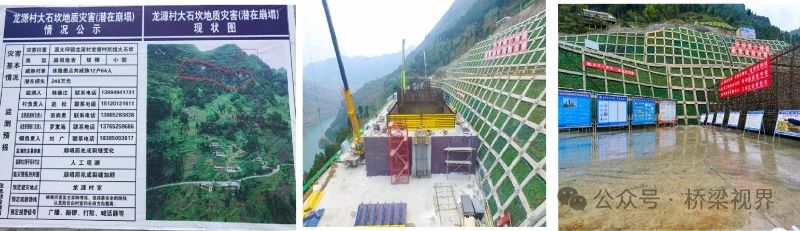
- Changing the cast-in-place box girder approach bridge to continuous rigid frame on the Renhuai side
The preliminary design of the approach bridge on the Renhuai side was a four-span (35+3×50) meter prestressed concrete cast-in-place box girder, constructed using steel tube scaffolding with a maximum height of 114 meters. If following the preliminary design plan, the 185m longitudinal range slope on the Renhuai side would require full ground scaffolding, necessitating multiple winding access roads and hoisting platforms, causing large-scale damage and disturbance to the entire slope. This slope is located in a government-declared geological disaster area, making this construction plan not only costly but also extremely risky for slope safety.
It has now been changed to a (48+80+48) meter three-span continuous rigid frame, reducing the number of piers and abutments and using the cantilever construction method, eliminating the need for large-scale ground scaffolding. This greatly reduces the number of platform excavations and winding access roads, decreasing the excavation range and volume.
Unlike conventional continuous rigid frames, to reduce the straight section of the side span, this project adopts an asymmetrical construction method where the middle span is closed first to complete the system conversion, then the cantilever sections of the side spans are constructed asymmetrically to the bridge abutment and cable tower cross beam, reducing the scaffolding for the cast-in-place straight sections.
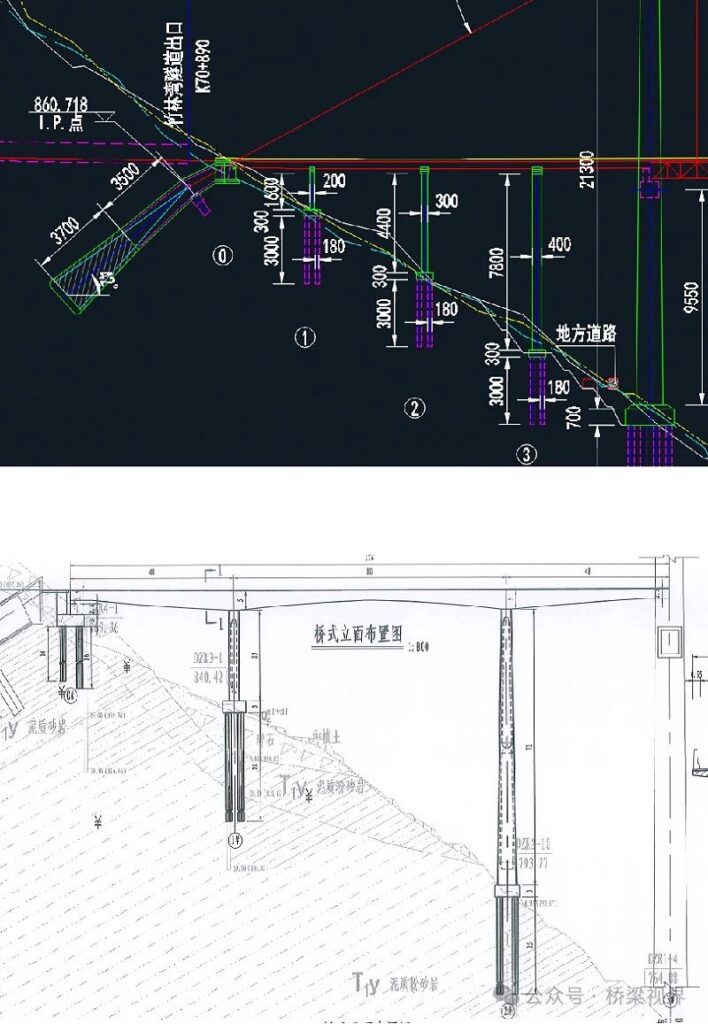
- Changing the #4 main tower from pile group in karst area to expanded foundation on the Tongzi side
The upper part of the bank slope on the Tongzi side is in a steep cliff state, while the lower part is in a staggered body state with well-developed unloading fissures and exposed limestone. According to detailed geological survey data, the karst influence range below the #4 main tower in the preliminary design was large and deep to 80 meters below the surface. The original design was a pile group foundation, requiring a large amount of karst filling treatment during construction, resulting in high construction costs and potential underground pollution from concrete filling materials, which could even pollute the water source protection area due to karst connectivity with the Tongzi River.
During the construction phase, through design optimization, the #4 main tower foundation was changed to an expanded foundation form. This not only reduced excavation but also allowed the rock layer cap to bear the bridge tower, canceling karst treatment and avoiding environmental pollution, fundamentally solving the environmental protection and soil and water conservation issues for the #4 main tower construction.
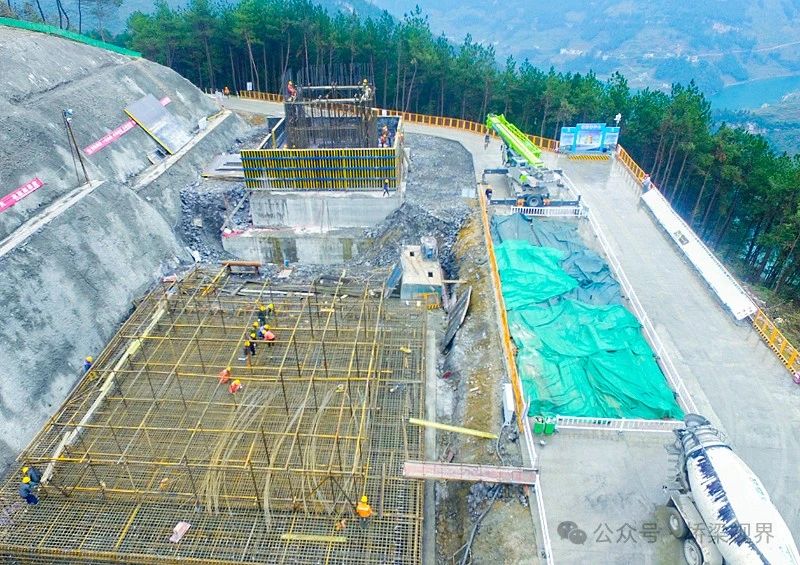
- Raising the gravity anchorage elevation on the Tongzi side to reduce mountain excavation
The preliminary design of the gravity anchorage on the Tongzi side was a buried type, with an excavation volume of about 220,000 cubic meters for the anchorage foundation pit. Through design optimization, the gravity anchorage elevation was raised overall, allowing it to meet structural force requirements through horizontal friction, anchorage self-weight, and rock embedment in front of the foundation. The excavation volume was reduced to about 60,000 cubic meters, and due to the elevation raise, the excavation slope range was also reduced, effectively lowering mountain excavation damage while reducing construction costs, meeting environmental protection and soil and water conservation requirements.
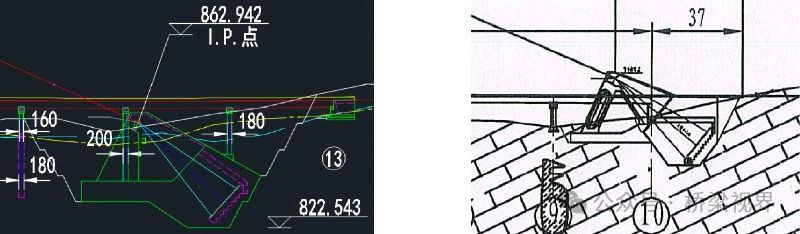
- Informationized and intelligent management
Information technology and intelligent technology are used in the green construction process to enhance personnel occupational health protection and site construction. A series of information technologies such as monitoring systems, real-name system for migrant workers, and mixing station systems are adopted for collaborative management.
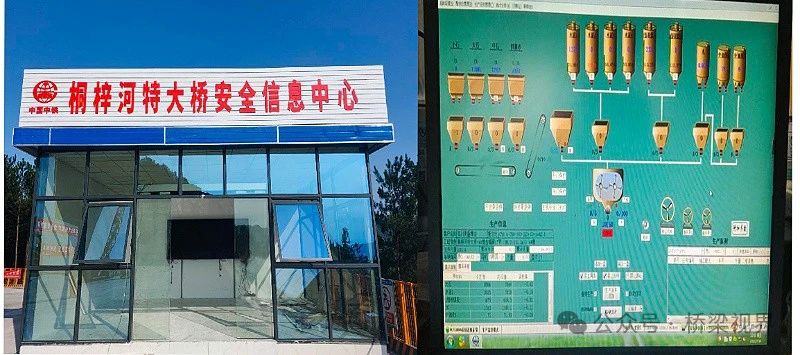
- Outward-tilting track trolley debris removal system
Due to geological reasons, the tunnel anchor portal engineering design plan was changed, delaying the overall project schedule by three months, affecting the bridge’s overall schedule goal. Unlike tunnel inclined shafts, the large-angle deep hole structure of the tunnel anchor poses extreme challenges to construction difficulty and efficiency, with the 47° excavation angle making it impossible for conventional equipment, personnel, and materials to self-stabilize and enter/exit the tunnel.
To this end, the track debris removal system was optimized to improve the work efficiency of tunnel excavation, striving to make up for the lost schedule. A new side-tilting mining car was adopted, using a double-track system to achieve side-tilting unloading while locking the car itself to prevent overturning, also solving the work stoppage problem of conventional mining cars waiting for dump trucks to receive materials. This system increases the strength of the support frame and the capacity of mining cars, using large winches as traction equipment. While meeting efficiency requirements, it does not require additional equipment investment, and all equipment is electrically driven, being low-carbon and energy-efficient, reducing fuel equipment input and environmental pollution.
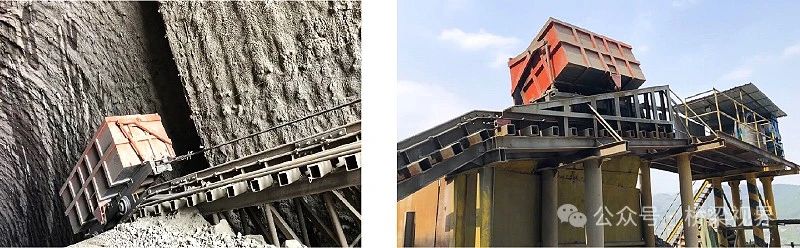
- “Antenna” “Ground wire” transport and hoisting system for tunnel anchors
After tunnel excavation is completed, about 16,000 cubic meters of reinforced concrete and anchorage systems need to be constructed inside the tunnel. Conventional hoisting equipment cannot operate in large-angle inclined tunnels. Our department set up winches and deflection devices on the platform outside the anchorage tunnel. In the early stage, materials inside the tunnel were transported using traction trolleys. In the later stage, steel structure supports and formwork were hoisted using the “antenna” hoisting system arranged along the tunnel top, solving the problem of material transport and hoisting inside the tunnel.
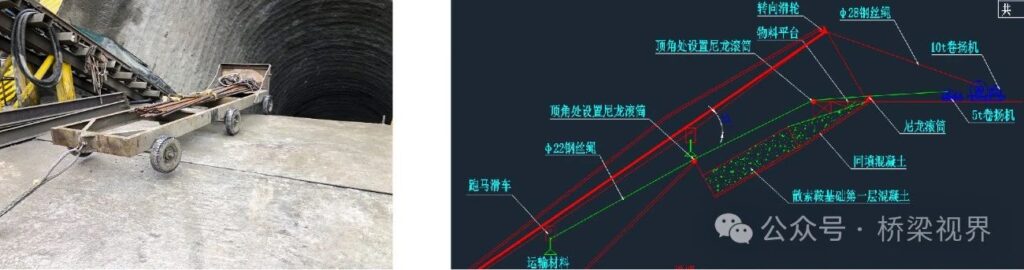
- Hoisting of scattered saddles in large-angle deep holes of tunnel anchors
Custom-made steel sliding frames were connected inside and outside the tunnel according to the angle of the tunnel anchor, allowing heavy saddle components to be transported from outside the tunnel to the design position inside the deep hole without large hoisting machinery. Then, a self-made hoisting system on a vertical lifting gantry was used to align and connect the scattered saddle body with the embedded system.
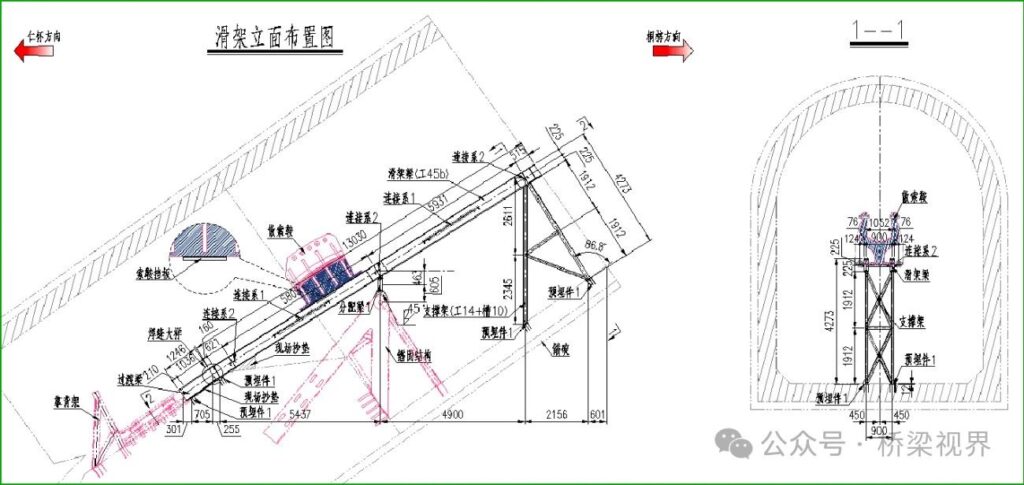
- New bubble mixed lightweight soil filling adopted for #3 main tower on the Renhuai side
The #3 main tower of the Tongzi River Grand Bridge on the Renhuai side is located on a steep slope, with the cap position in a half-fill half-excavation area. The platform has a vertical height of 15m on the overhang side towards the span, with farmland and villages immediately below. Conventional platform schemes involve excavating terraces on the slope and casting heavy concrete retaining walls for protection. However, the overall bank slope geological conditions on the Renhuai side are poor. On one hand, the foundation of heavy retaining walls requires a large excavation area, greatly disturbing the slope foot and posing safety risks during excavation. On the other hand, the heavy retaining wall itself would exert a significant vertical load on the unstable steep slope, increasing the risk of slope sliding, which does not align with the environmental protection and water conservation intentions of this project.
In the construction design, the method of filling bubble mixed lightweight soil retaining walls was adopted to form the #3 main tower platform on the Renhuai side. Bubble mixed lightweight soil is a new type of microporous lightweight eco-friendly material with characteristics of lightweight, self-standing, self-compacting, adjustable density and strength, easy construction, thermal insulation, and environmental friendliness. Through the implementation of this bubble mixed lightweight soil retaining wall, this project reduced foundation excavation and gravity load on the foundation, creating technical construction highlights such as compression and overturning resistance, durability, safety, and rapid construction of the retaining wall under extreme conditions during flood seasons.
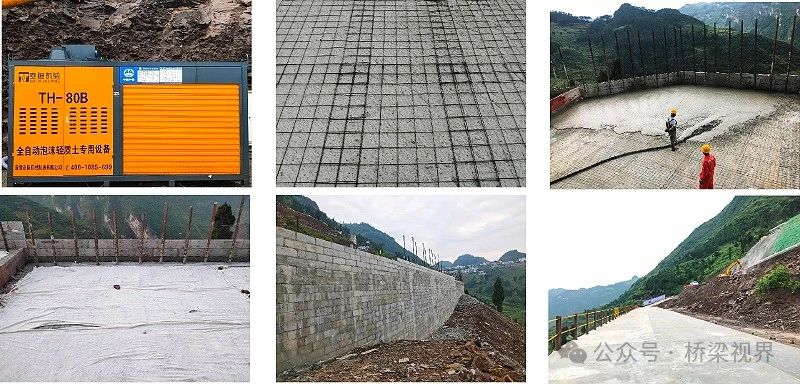
- Climbing formwork safety design
The cable towers of the Tongzi River Grand Bridge are inclined in four directions and inward, while the climbing formwork frame needs to maintain a relatively vertical state to ensure balanced and stable force bearing. This usually requires changing tracks midway for most inclined towers, but changing tracks means high-altitude system conversion and increased hidden dangers in major hazardous processes (high-altitude frame disassembly and assembly).
On one hand, this project modified the climbing formwork frame. By connecting the chamfered section formwork frame with the straight face section as a whole to balance the counterweight of the frame, it allows the frame and climbing track to be eccentrically arranged in the early stage while ensuring safety, enabling the climbing formwork to climb directly from the tower base to the top without the need for the conventional high-risk track change for inclined towers. On the other hand, this project’s climbing formwork adopted the latest perforated steel plate protective net to enclose the entire climbing platform, with high strength, good wind resistance, strong enclosure, and an attractive appearance. All working platforms are equipped with centralized storage boxes and fire extinguishing devices, and all holes and gaps are closed with high-strength hinged flip boards, reducing high-altitude operation risks to a minimum from a management behavior perspective.
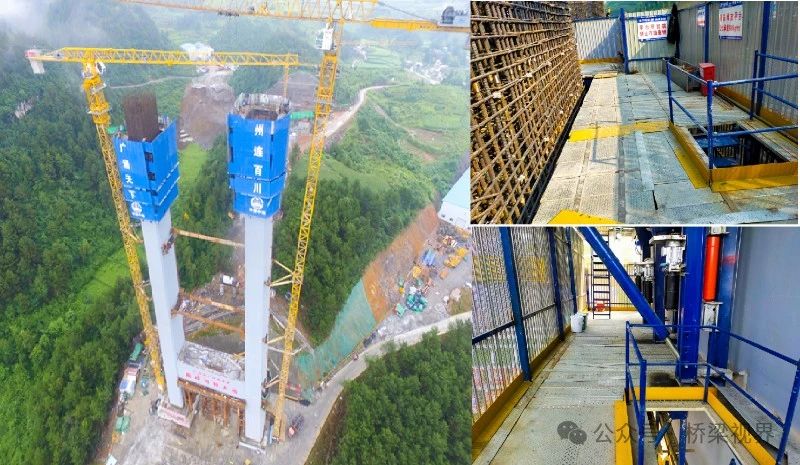
- High tower spray curing
After connecting the water supply pipe to the climbing formwork frame, it follows the frame to connect to the sprinkler pipes, which are arranged in a circle along the top platform of the climbing formwork frame. Using 3.5cm soft pipes with multiple evenly distributed spray holes. When concrete pouring is completed and needs curing, simply turn on the sprinkler system switch, and the entire system starts running, achieving the curing effect. The self-made sprinkler system saves labor, reduces materials, is easy to install and repair, saves water, and avoids the occurrence of missed curing, truly realizing all-weather, all-around spray curing, achieving “on-demand curing”.
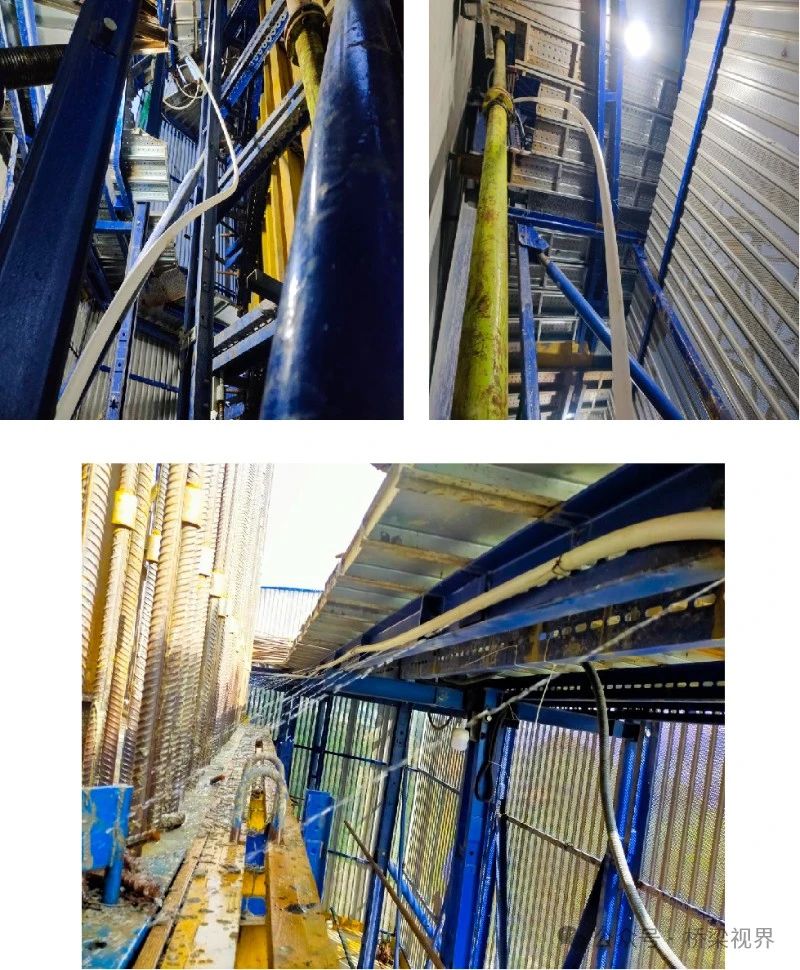
- “Quick and easy closing net” for anchorage closure strips
The anchorage of this project is 27.72m high, with three closure strips. Conventional anchorage closure strip construction methods use ordinary wooden or steel formwork for segmented pouring, but the resulting narrow spaces lead to a huge amount of chipping work that is difficult to guarantee in quality. During the initial planning of the Tongzi River Grand Bridge construction, through economic comparison and scheme comparison, our department chose to adopt a new type of formwork material – quick and easy closing net. This material has certain strength and can completely replace ordinary formwork when combined with straps and tie rods. Its wrinkled shape and dense mesh structure characteristics allow it to be firmly embedded with concrete, and after concrete formation, it replaces chipping construction, even making the bonding effect of closure strip concrete superior to conventional construction joint chipping.
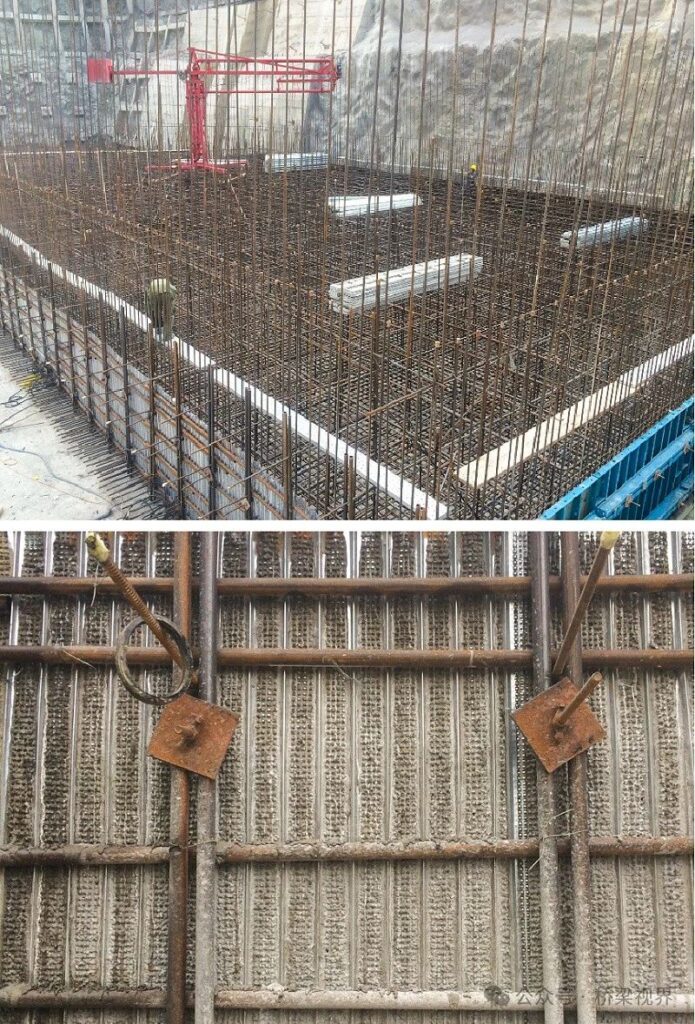
- Traction system and hoisting wire ropes use galvanized wire ropes
The cables used in the traction system and hoisting system of suspension bridges are usually traditional oil-immersed wire ropes, with the surface covered in grease for cable protection. However, as the temperature rises, the oil on the cables will drip onto the structures below, causing pollution that is difficult to clean. This project plans to use galvanized oil-free wire ropes for the cable system, avoiding pollution to structures and the environment from cable oil during the construction of the upper structure.
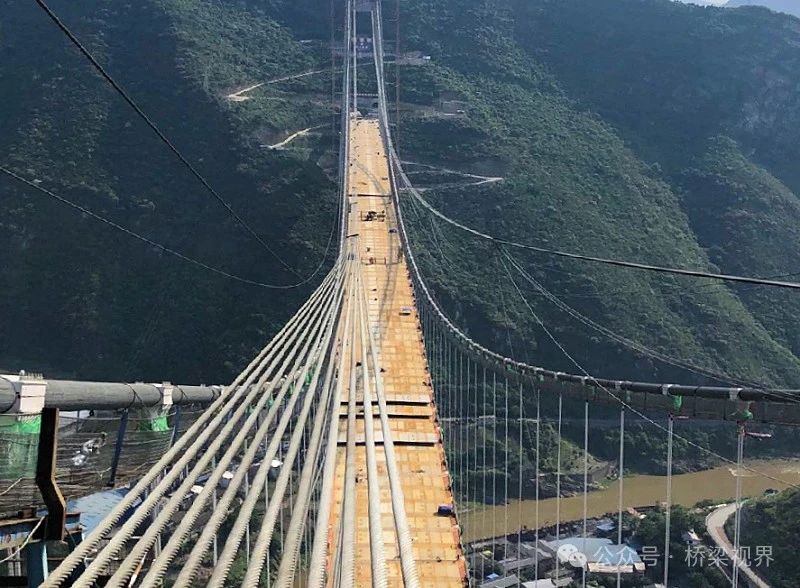
- Pre-forming of cable strands in the factory
When installing a single cable strand into the saddle, it needs to be reshaped from a regular hexagonal state to a quadrilateral state before being locked in the saddle groove. On-site reshaping is difficult to ensure precision and has low efficiency. In this project, cable strands are accurately measured and positioned in the manufacturing factory, and the “hexagon to quadrilateral” pre-forming of cable strands is precisely completed through forming equipment in the factory, allowing direct installation into the saddle on-site.
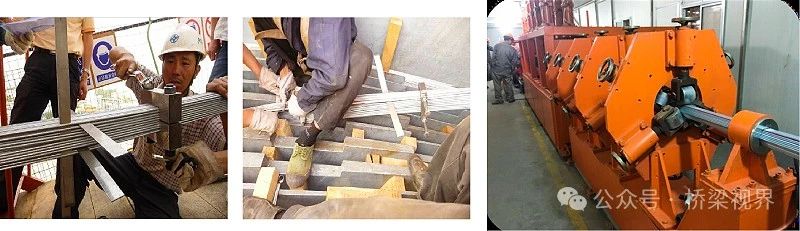