Project Profile
Name: Zhenba (Sichuan-Shaanxi Border) to Guang’an Expressway Tongjiang to Guang’an Section C Contract Segment C10 Project Department (Baimaqujian Extra-large Bridge)
Birthday: Under Construction
Birthplace: Sichuan
Length: Main span of the bridge 418.8m, net span 390m
Type: Concrete-filled steel tube arch bridge with suspended deck
Features: The construction of the concrete-filled steel tube arch bridge for the Baimaqujian Bridge has technical features such as large single-segment hanging weight of the arch rib (151T), long hanging segment size of the arch rib (37.5m), and great difficulty in mid-air turning of the arch rib segments. The designed span of the bridge ranks among the top of under-construction bridges of the same type.
Construction Unit: Sichuan Zhenguang Expressway Co., Ltd.
Design Unit: Guangdong Provincial Communications Planning and Design Institute Group Co., Ltd.
Construction Unit: Sichuan Road & Bridge Co., Ltd.
The Baimaqujian Extra-large Bridge starts from Baimavillage, Guang’an City and ends at Huchengtown, Guang’an City, spanning across the Qujian River (Siqutan Reservoir area). The designed bridge span combination is: (3×30+40)m prestressed concrete T-beam + 1×418.8m concrete-filled steel tube arch bridge with suspended deck + (40+2×30)m prestressed concrete T-beam. The bridge starts at pile number K271+136.1 and ends at K271+793.9, with a total length of 657.8m. The total width of the bridge is 29.5m. The arch ribs are variable cross-section steel tube concrete truss structures, with a net span of 390m, a calculated rise-to-span ratio of 1/4, an arch axis coefficient of 1.65, a crown section radial height of 6.5m, a springline section radial height of 12.0m, a rib width of 4.0m, and an arch rib center-to-center distance of 31.0m. The φ1200mm chord tubes inside the arch ribs are filled with C60 self-compacting and shrinkage-compensating concrete. To enhance the lateral connection of the arch ribs, C60 self-compacting and shrinkage-compensating concrete is cast at the hanger locations in the upper lateral bracings.
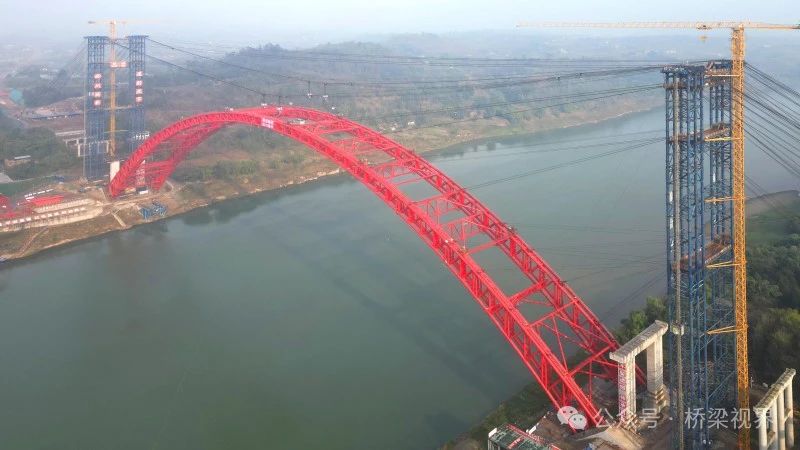
Unique Aspects
1. The two banks of the bridge are greatly affected by geological and topographical conditions, especially the area near the larger pile number, which is affected by a 35KV high-voltage line from a national power company and fish ponds, causing great difficulty in the design of the cable-stayed erection system. After repeated studies and verifications by the company and the project technical team, a construction scheme with an asymmetric layout of the cable-stayed erection system was adopted for the first time, with water-to-cable angles of 45° and 37.5° on the two banks respectively.
2. The bridge spans across the Qujian River, and the bridge construction site is within the water source protection area and precious fish species protection area of Guang’an, requiring high environmental protection standards.
3. The entire arch rib of the bridge is designed with 36 segments, with segment lengths ranging from 25m to 37.5m and net hanging weights from 95T to 151T. The segments have the technical features of large hanging weight, long single structure, and great difficulty in mid-air turning.
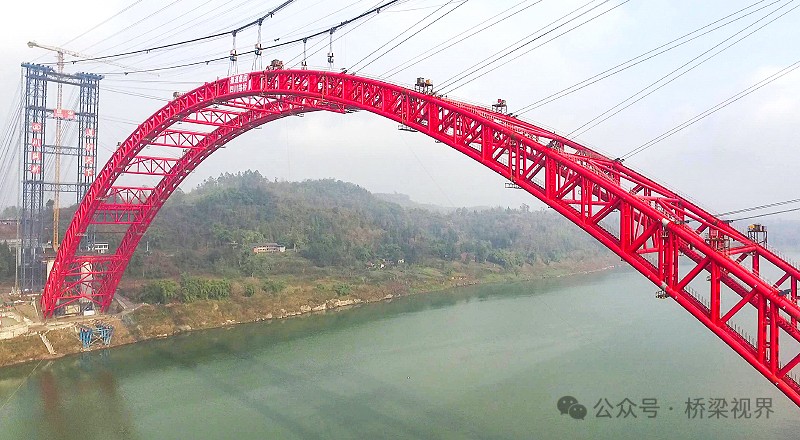
During the construction of the Baimaqujian Extra-large Bridge, the project management team carried out 6 process and management innovations in the entire cable-stayed erection process:
1. Optimization and improvement of the number of main hoisting and main pulling saddles in the cable-stayed erection system: The project technical team innovatively optimized and improved the traditional approach of placing one saddle every 30m, changing it to one saddle every 80m. For the entire bridge, only 12 saddles were used on both sides of the river, reducing the number by 20 compared to the traditional arrangement while achieving the same effect, saving construction costs and greatly reducing installation risks.
2. Establishment of a smart monitoring and detection center: The project introduced an intelligent monitoring system for cable-stayed erection. The entire arch rib hoisting operation was carried out through centralized control, changing from the traditional local control to remote control, requiring only 2 operators in the monitoring center to complete the hoisting operation. At the same time, the system continuously monitored and detected key data indicators such as stress, deformation, and cable tower offset, greatly reducing the number of workers and associated labor costs while also lowering safety risks, ensuring the safety and stability of the system.
3. Innovation in the transportation and turning process of the steel tube arch: The arch rib segments were assembled horizontally at the prefabrication yard and transported horizontally. The project technical team abandoned the traditional construction method of directly building a steel bridge across the Qujian River and then using a gantry crane to load the segments onto a ship for transportation and installation. Instead, they innovatively adopted an approach where a U-shaped pit was excavated at one end of the prefabrication yard, and the segments were moved longitudinally and transversely using a specially designed detachable double-layer trailer to the designated hoisting location under the arch, greatly reducing construction difficulty and saving costs.
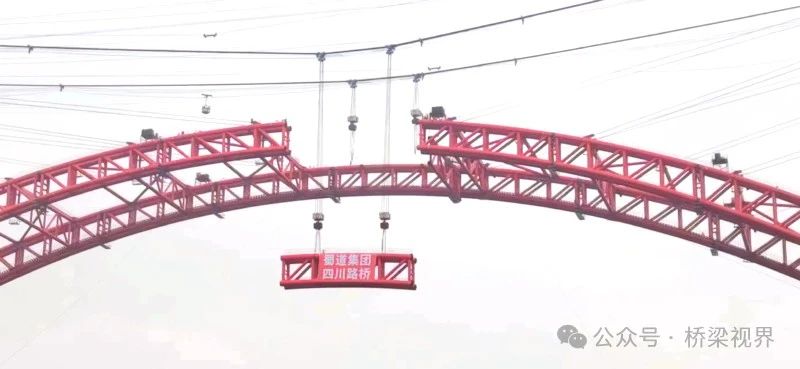
4. Full prefabrication of cable tower assembly and tower head assembly: The entire cable-stayed erection system, including the main towers, wind bracings, cross beams, and tower heads, adopted full prefabrication for construction, greatly improving installation efficiency and reducing high-altitude work time. Workers only needed a hammer and an electric wrench to complete the cable tower assembly. The welding-free cable tower assembly enhanced the overall safety of the towers and facilitated reuse, reducing construction costs.
5. Application of self-drilling anchors for back-stay cables and back-wind-resistant cables: According to conventional methods, anchor connections typically use two ordinary anchors (conical hole anchors) for connection, which are then fixed on both sides using a pressing head. For this project, based on actual needs and quantities, and considering the characteristics of ordinary anchors and the desired results, the project directly required the manufacturer to custom-produce straight-hole anchors for all the required anchors. This way, during the anchor connection process, only one anchor was needed, greatly reducing the number of anchors and indirectly saving project costs.
6. Use of steel beam transfer girders instead of reinforced concrete transfer girders: In the entire cable-stayed erection system, the transfer girders for the anchor systems are generally made of reinforced concrete. However, based on the force structure and force transfer method, the project used reusable steel beam transfer girders instead of reinforced concrete transfer girders, which was validated throughout the hoisting process. The successful use of steel beam transfer girders provides a reference for future cable-stayed erection systems to eliminate the use of reinforced concrete transfer girders, greatly reducing costs and environmental pollution.