On July 30th at 00:13, the control project for the Guinan High-Speed Railway’s entry into Guiyang Hub – the curved beam of the Hulupo Grand Bridge on the Ma-Da Left Line – was precisely connected with the bridge structures at both ends above the Shanghai-Kunming Railway. This marks the successful completion of the most technically challenging key node project on the entire line. It is China’s first railway bridge featuring a large-span, heavy-tonnage curved beam rotation construction atop a high pier.
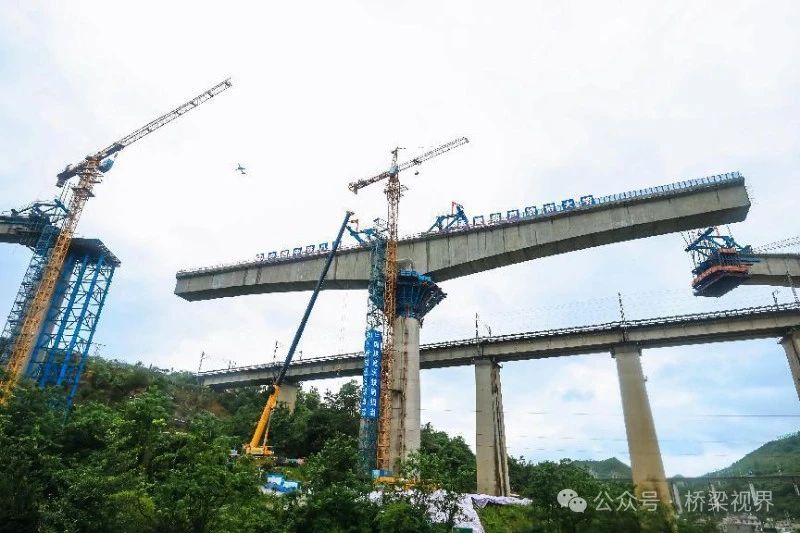
The Hulupo Grand Bridge is located in a valley beneath the flight path of Guiyang Longdongbao Airport, spanning over the operational Shanghai-Kunming Railway line. With a total length of approximately 1,048 meters and 22 piers and abutments, the average pier height exceeds 19 meters. Due to the narrow terrain with significant elevation changes, the on-site construction environment was complex. To effectively ensure the construction schedule and safety quality, the bridge adopted a “build first, rotate later” approach. Before rotation, the bridge was constructed parallel to the Xiaobi Grand Bridge of the Shanghai-Kunming Railway, with the edge of the beam 14.1 meters from the railway edge.
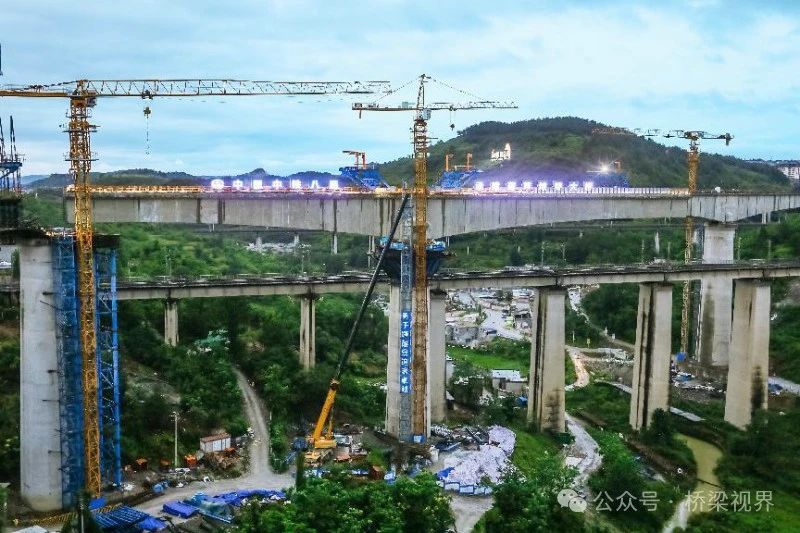
To minimize impact on the operational line, a 20-meter short-arm tower crane was used during construction to reduce the working radius. Simultaneously, horizontal carriers were equipped on the bridge deck to complete on-site material stacking and transportation. Real-time monitoring of key construction processes, data, and the use of large machinery near the railway line was strengthened to minimize the impact on the existing line and surrounding environment. According to the project’s technical director, the rotated beam at Pier No. 8 has a pier height of 42.5 meters, a beam length of 142 meters, a width of 8.5 meters, weighing 8,350 tons, with a curve radius of 1,600 meters.
Real-time monitoring of bridge data was conducted during the rotation process. The project employed an intelligent visual monitoring system to track rotation parameters in real-time, monitoring critical information such as wind speed, wind direction, rotation speed, and the spatial attitude of the beam. Through “full-process visualization and intelligent control,” early analysis and warning were achieved, controlling the irregular “building block” assembly error to millimeter-level precision.