Project Files
- Name: Zangkexiang Super Major Bridge
- Birthday: Under construction
- Place of Origin: Guizhou Province
- Length: Total bridge length 1849m, main span 1080m
- Type: Suspension bridge
- Features: Located across a V-shaped valley, with complex terrain, high environmental protection requirements, high difficulty of excavating large-diameter pile foundations, many times of pouring large-volume concrete, high frequency of high-altitude operations, high safety risks
- Construction Unit: Guizhou Naqing Expressway Co., Ltd.
- Design Unit: CCCC Second Highway Consultants Co., Ltd.
- Construction Unit: Guizhou Highway Engineering Group Co., Ltd.
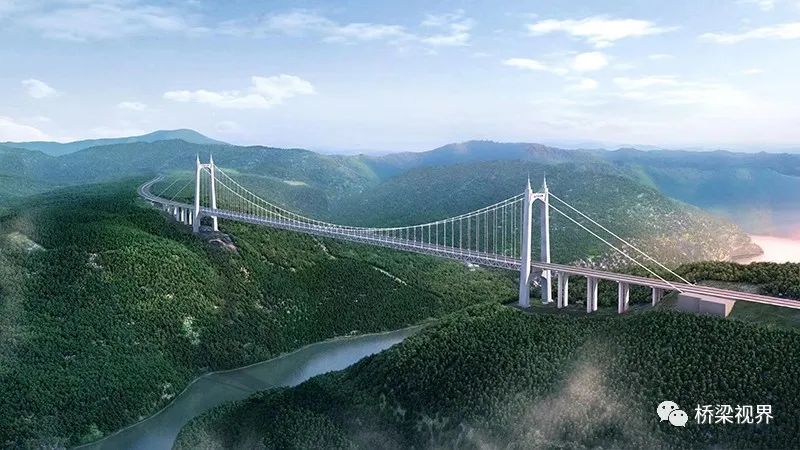
My Uniqueness
1. Project Difficulties
The Zangkexiang Super Major Bridge is one of the main control projects of the Naqing Expressway (the only suspension bridge), spanning the Beipanjiang River (Zangkexiang Scenic Area). The main towers are located on the slopes of the V-shaped valley, with the bridge deck 313m above the water surface. The construction process has high environmental protection requirements and difficulties.
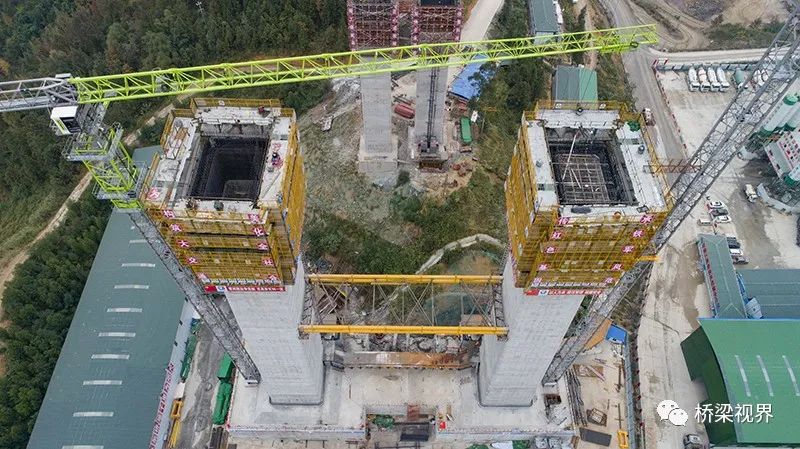
- The maximum pile diameter of the main tower foundation is 3.8m, using manual excavation pit construction method. The excavation process has high safety requirements, and it is difficult to pour the pile concrete.
- The main tower piers and gravity anchors require 113,000 cubic meters of concrete. When the weather is hot (up to 41°C), the single large concrete pour has a large volume, making it difficult to control the hydration heat.
- The main tower height reaches 248.1m. As a four-side sloping A-shaped inclined tower, the control of the tower line shape has high requirements, and the construction process has a high risk level. The lower cross beam has a height of 101.5m, a span of 31.6m, and a weight of 4,074 tons, with great construction difficulty.
- Since the main towers on both banks are located on the slopes of the V-shaped valley, it is difficult to select an assembly site for the steel truss girders on the Nayong side, where the slope reaches 64 degrees. The maximum single hoisting weight is 231 tons, which is a large weight.
- The approach bridge on the Qinglong side is designed as an 8-span 60m steel-concrete composite beam structure, making the steel beam installation difficult.
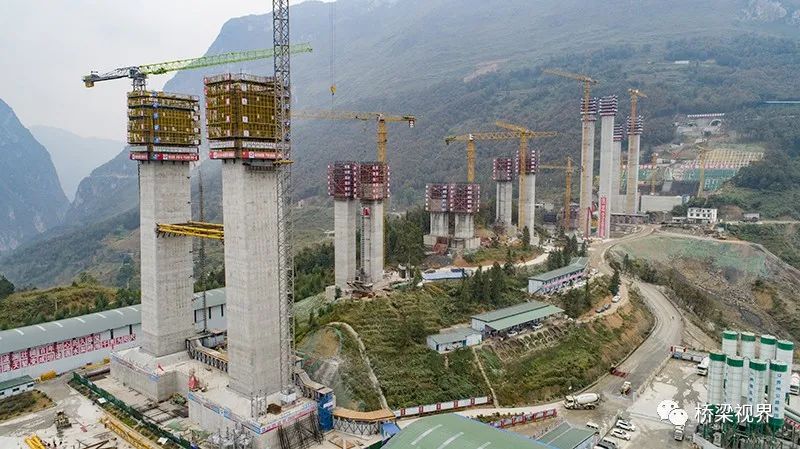
2. Innovations
- Based on the lower cross beam of the main tower on the Qinglong side, the “Mechanical Performance Analysis and Construction Method Innovation of the Super-large Span Poured-in-place Baret Support System in Mountainous Areas” project was established.
- Based on the construction of the steel-concrete composite beam of the approach bridge on the Qinglong side, the “Integrated Technology Research on Continuous Pushing Construction of Large-span Steel Beams without Guide Beams” project was established.
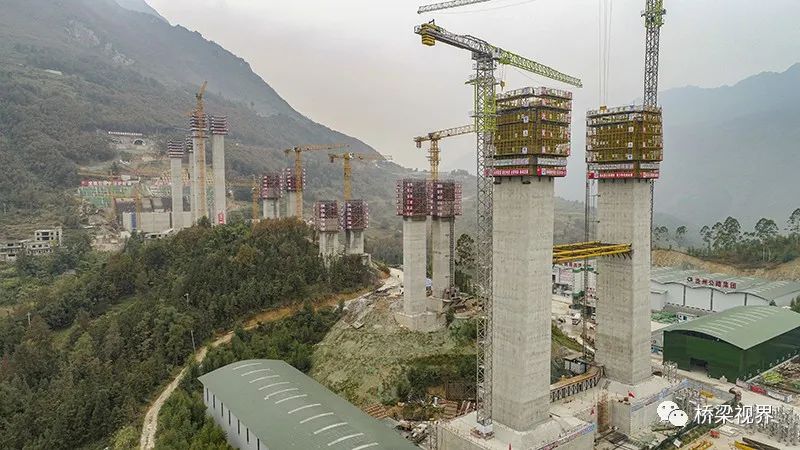
▲ Overall view of Qinglong side
- The main cables adopt a new zinc-aluminum-rare earth alloy-coated main cable steel wire product and process, replacing the traditional zinc-aluminum alloy products and processes, breaking through the key technical bottleneck of high-strength steel wires for suspension bridge main cables. It has excellent corrosion resistance and fatigue resistance performance, with all test indicators higher than the current national and industry technical standards.
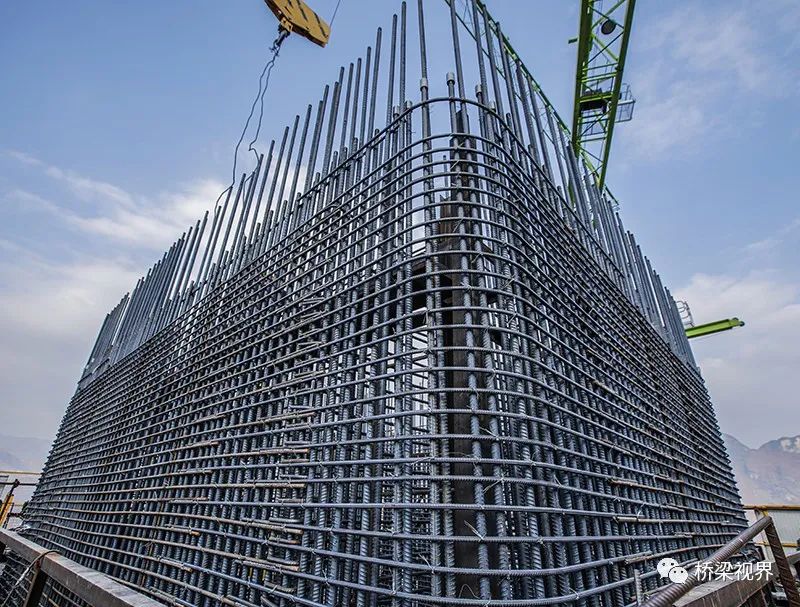
▲ Reinforcement installation of main tower shaft
- For the first time in the bridge industry internationally, high-strength zinc-aluminum-rare earth alloy-coated sealed steel wire ropes are used as suspenders, replacing traditional parallel wire suspenders and eliminating the PE sheath of traditional parallel wire suspenders. The 1960-grade Z-shaped wire sealed rope suspenders have high strength, excellent corrosion resistance, and fatigue resistance performance, filling a gap in this field.
- A new “safety score supermarket” safety management model was proposed, effectively engaging all employees in safety management, enhancing their enthusiasm and safety awareness, and being widely promoted.
- Regionalized enclosed construction management was implemented for the highway project, with “employee real-name access channels” and face recognition systems installed to monitor the information of construction workers in the enclosed areas in real-time.
- During construction, many quality optimization and micro-innovation processes were summarized and proposed (super-large diameter pile foundation manual excavation vehicle crane spoil removal technology, mobile formwork core drilling platform innovation technology, large-volume concrete temperature control technology, structural chamfer angle steel quality protection technology, pier column construction appearance quality protection technology (geotextile wrap mini-skirt for high piers), forced vertical alignment control technology for high piers, safety management score supermarket innovation, real-name access channel management innovation for work areas).
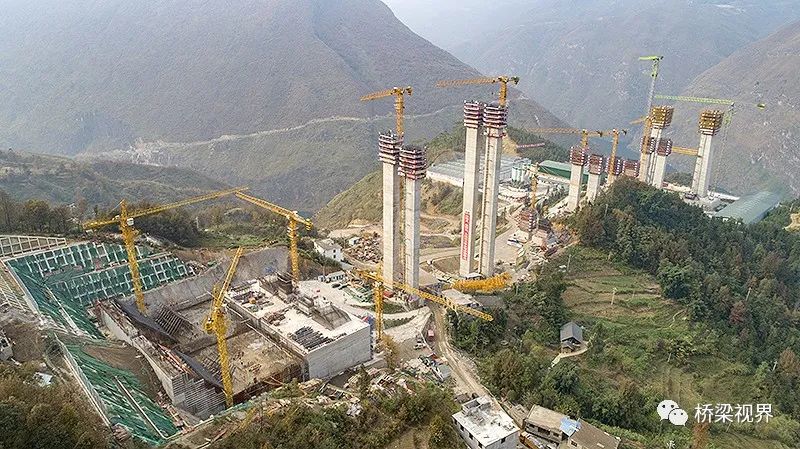
- The “Mechanical Performance Analysis and Construction Method Innovation of the Super-large Span Poured-in-place Baret Support System in Mountainous Areas” greatly broke through the span limit of the Baret support system, effectively promoted the innovation of high pier support systems, and greatly reduced construction costs.
- The “Integrated Technology Research on Continuous Pushing Construction of Large-span Steel Beams without Guide Beams” proposed a complete set of pushing construction techniques without guide beams, enriching the choices of pushing construction methods and having milestone significance for the development of pushing construction.